Assembling a PCB board is a crucial skill for anyone venturing into electronics. It combines precision, creativity, and technical know-how to bring designs to life. If your project also involves wiring and connectors, custom cable assembly can be essential to ensure secure and reliable connections. This article will guide readers through the essential steps and best practices, ensuring a successful assembly process that leads to reliable and efficient electronic devices.
Understanding PCB Boards
Understanding PCB boards is essential for anyone involved in electronics. These boards play a crucial role in connecting various electronic components, ensuring reliable operation in devices.
What Is a PCB Board?
A PCB (Printed Circuit Board) is a flat board made from insulating material that hosts conductive pathways. These pathways, etched from copper sheets, enable electrical connections between components such as resistors, capacitors, and microcontrollers. PCBs serve as the backbone of electronic devices, facilitating communication between various parts and ensuring proper functionality.
Types of PCB Boards
Several types of PCBs exist, each designed for specific applications. The main categories include:
- Single-Sided PCBs: These boards contain one layer of conductive material. They accommodate simpler circuits and are cost-effective for basic electronic devices.
- Double-Sided PCBs: These boards feature conductive layers on both sides, allowing for more complex designs and higher component density. They support more intricate circuits compared to single-sided options.
- Multilayer PCBs: Comprising three or more conductive layers, multilayer PCBs facilitate advanced connectivity in sophisticated devices. They enable compact designs, making them suitable for devices like smartphones and computers.
- Flexible PCBs: These boards use flexible materials, allowing for bending and twisting without damaging the circuitry. They are ideal for compact, portable devices and applications requiring dynamic configurations.
- Rigid-Flex PCBs: Combining rigid and flexible circuit designs, rigid-flex PCBs provide enhanced durability and application flexibility. They are commonly used in medical devices and aerospace technology.
Understanding the different types of PCBs helps in selecting the appropriate design for specific projects, showcasing the versatility essential in modern electronics.
Tools and Materials Needed
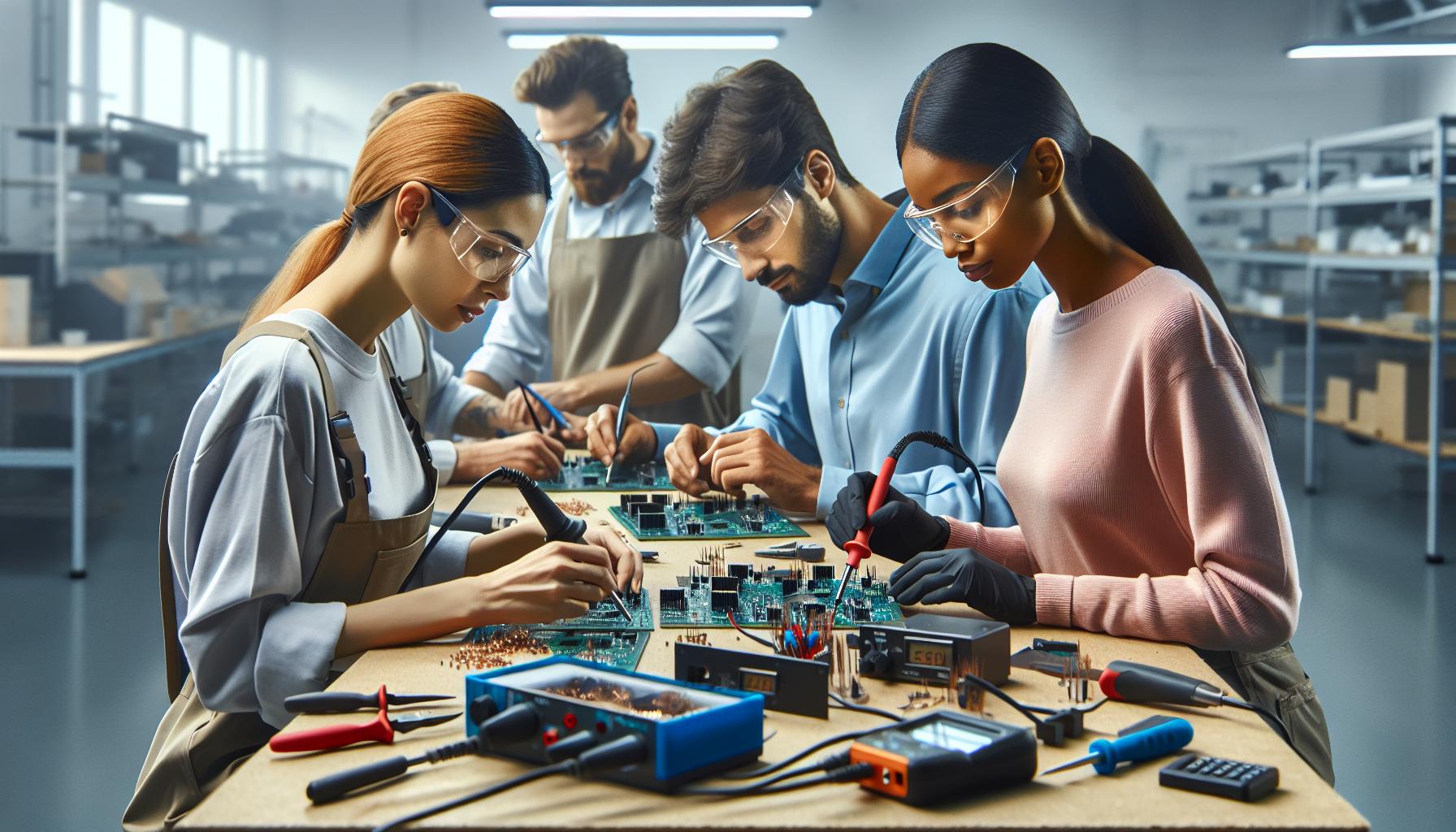
Assembling a PCB requires specific tools and materials to ensure efficiency and precision. Below is a detailed list of essential items necessary for the task.
Essential Tools
- Soldering Iron: A critical tool for melting solder and joining components. A fine tip provides better control for precision work.
- Solder: Use lead-free solder for environmental safety and to ensure a reliable connection. A diameter of 0.5 mm works well for most PCBs.
- Wire Cutters: Necessary for trimming excess leads after soldering, ensuring a neat finish.
- Tweezers: Offer precision when placing small components on the board. Anti-static tweezers reduce the risk of damaging sensitive parts.
- Multimeter: Essential for testing connections and ensuring circuit integrity. It helps diagnose issues during assembly and troubleshooting.
- Desoldering Pump: Useful for correcting mistakes and removing excess solder. It creates a vacuum to suck up molten solder.
- Adjustable Workbench Magnifier: Facilitates detailed work by magnifying small components and connections.
- Static-Free Mat: Protects the PCB and components from static electricity during assembly.
- Printed Circuit Board (PCB): The foundation of the assembly, selected based on design specifications. Choose a type compatible with the project requirements.
- Electronic Components: Includes resistors, capacitors, diodes, and integrated circuits. Ensure each component meets the design’s specifications and ratings.
- Soldering Flux: Enhances solderability and improves the quality of joints. A rosin-based flux is commonly used for electronics.
- Heat Shrink Tubing: Provides insulation for exposed wires and connections. It prevents short-circuits and insulation failures.
- Connectors: Necessary for joining different circuit sections. Choose based on the design needs for durability and ease of connection.
- Labels or Markers: Useful for marking connections and component placement for future reference. Clear labeling aids in troubleshooting and maintenance.
Step-by-Step Guide to Assemble PCB Board
Assembling a PCB board requires careful attention to detail and a systematic approach. Follow these steps to complete the process effectively.
Designing the PCB Layout
Designing the PCB layout sets the foundation for assembly. Utilize PCB design software to arrange components optimally on the board while ensuring minimal interference and proper spacing. Focus on creating clear pathways for electrical connections. An organized layout reduces errors during assembly and enhances the performance of the final product.
Sourcing Components
Sourcing components is crucial for successful assembly. Identify all necessary electronic parts as specified in the PCB design. Use reputable suppliers to ensure quality and reliability. Verify the specifications of each component, such as resistance values for resistors and capacitance for capacitors. Consider purchasing extra components as backups to avoid delays during assembly.
Preparing the PCB
Preparing the PCB involves cleaning and inspecting the board before assembly. Use isopropyl alcohol and a lint-free cloth to remove any dust or residues. Inspect the board for defects, such as scratches or discoloration, which can impact performance. Ensure the board is free from static electricity by using a static-free mat during the preparation phase.
Assembling the Components
Assembling the components is a meticulous process. Begin by placing each component in its designated spot according to the layout. Use tweezers for small components to avoid damaging them. Clearly identify component leads and ensure correct orientation, especially for polarized components like capacitors and diodes. Confirm each component’s placement before proceeding to soldering.
Soldering Techniques
Soldering techniques are critical for creating strong connections. Heat the soldering iron to the appropriate temperature, usually around 350°C (662°F). Apply solder only to the connection point, ensuring it fills the joint without overheating components. Different techniques, such as through-hole soldering or surface-mount soldering, require different approaches, so choose the method that best fits the components used. After soldering, inspect each joint for clarity and strength to ensure reliable electrical connections.
Common Mistakes to Avoid
Assembling a PCB requires attention to detail. Understanding common mistakes can prevent issues that compromise device functionality.
Incorrect Component Placement
Incorrectly placing components on a PCB leads to significant operational problems. Components can short-circuit or fail to connect, disrupting signal flow. Check the specifications for each component before placement. Follow the schematic closely to avoid errors. Double-check orientation for polarized components, such as capacitors and diodes. Ensure proper alignment with pads to facilitate effective soldering. Finally, use a magnifying tool during assembly for better visibility.
Soldering Issues
Soldering problems can undermine the integrity of the connections. Insufficient heat or improper solder technique creates weak joints that may break. Use a soldering iron at the recommended temperature, typically between 350°C (662°F) and 370°C (698°F). Apply solder until it flows smoothly around the pad and component lead. Avoid over-soldering, as this can create solder bridges between adjacent pads, causing short circuits. Inspect each joint with a magnifying glass to ensure clean, solid connections.
Conclusion
Mastering PCB assembly is an essential skill for anyone passionate about electronics. With the right tools and a systematic approach, it’s possible to create reliable and efficient devices. Attention to detail during each step of the process ensures that components are placed correctly and soldered with precision.
Avoiding common mistakes can significantly improve the quality of the final product. By following best practices and understanding the various types of PCBs, individuals can tailor their projects to meet specific needs. Assembling a PCB not only fosters creativity but also builds confidence in one’s technical abilities, paving the way for future innovations in electronics.
Frequently Asked Questions
What is PCB assembly?
PCB assembly is the process of putting together a Printed Circuit Board (PCB) by placing and soldering electronic components onto the board to create functional electronic devices. It combines precision, creativity, and technical knowledge to ensure reliable connections and effective designs.
What are the main types of PCBs?
The main types of PCBs include single-sided, double-sided, multilayer, flexible, and rigid-flex boards. Each type is designed for specific applications based on factors like component density, size restrictions, and required flexibility.
What tools are needed for PCB assembly?
Essential tools for PCB assembly include a soldering iron, lead-free solder, wire cutters, tweezers, a multimeter, a desoldering pump, an adjustable workbench magnifier, and a static-free mat. Each tool ensures precision and efficiency during the assembly process.
How do I design a PCB layout?
To design a PCB layout, use design software to optimize the arrangement of components for clear electrical pathways. This step is crucial in ensuring that all components function correctly and can communicate properly within the circuit.
What common mistakes should I avoid during PCB assembly?
Common mistakes in PCB assembly include incorrect component placement, inadequate soldering techniques, and misreading schematics. To avoid these, double-check specifications, use magnifying tools for visibility, and inspect solder joints for reliability before finalizing your assembly.